The use of axial flux motors is gaining traction across industries, particularly in the electric motor space.
Axial flux motors or pancake motors are mechanically configured to provide specific advantages when compared to ubiquitous radial flux motors. By design, the space between the rotor and stator (described in technical terms as the direction of magnetic flux between the two) in an axial flux motor is aligned parallel to the axis of rotation. Horizontal Full Servo Embedding Machine
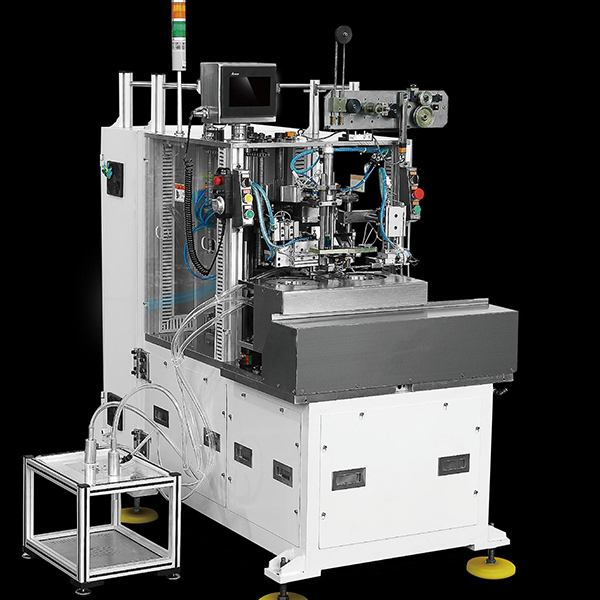
Its counterpart, the radial flux motor , is named for the magnetic field generated by the stator windings that moves radially across the air gap between the stator and rotor, and induces a torque that turns the rotor. Despite the ubiquity of radial flux motors, both types offer characteristic strengths and weaknesses, depending on the application.
According to Infinitum’s chief strategy officer, Bhavnesh Patel, axial flux propulsion is gaining ground in the EV space due to specific design form factors that allow the motor to sustainably power passenger and commercial electric vehicles. Axial flux motors, he said, are touted for their ability to generate more torque and power density than radial flux motors, and occupy less space based on the configuration.
Patel told Machine Design during a one-on-one briefing that Infinitum will roll out the next generation of its axial flux motor (Aircore EC motor) at AHR Expo in Chicago (Jan. 22-24, 2024).
Aircore EC is a high-efficiency motor designed to sustainably power commercial and industrial applications—such as HVAC fans, pumps and data centers—with less energy consumption, reduced emissions and reduced waste.
READ MORE: Custom Motor Design: SaaS Platform Brings Flexibility to PCB Stator Design
Covered by 43 issued patents and 48 pending patents, the new motor replaces the heavy, copper wound iron stator found in traditional motors with a lightweight, printed circuit board (PCB) stator that is 10 times more reliable, 10% more efficient, and 50% smaller and lighter, noted Infinitum’s briefing notes.
Every motor is built around a stator and rotor. “A stator is essentially copper wire wrapped around iron; you can run current through that copper and it creates magnetic field,” explained Patel. “The innovation that we have is that we eliminated the iron within that stator and, instead of using copper wire, we etched the copper on multiple layers of a printed circuit board. And that results in is a number of benefits.”
In mobility applications, for example, PCB stators offer promising performance and efficiency benefits due to superior heat mitigation and high power density. Another distinguishing factor is that it uses 66% less copper than conventional motors, Patel said. Replacing the iron core with a PCB stator has further resulted in a reduction in mechanical losses, greater efficiency gains, and noise and vibration reductions.
With the PCB stator design, said Patel, the motor can achieve up to four to five times the current density of a conventional, liquid cooled motor using a liquid cooling technique that allows the coolant to be in direct contact with the stator, mitigating heat across a larger surface area, enabling high overload capability and extended life.
The startup characterized the Aircore EC motor system as an integrated variable frequency drive that delivers upwards of 93% system efficiency, as well as class-leading power and torque density in a low-footprint package that is 20% lighter than the previous version.
The combination motor and variable frequency drive or VFD (“essentially the electronics that drive the motor”) is a defining feature. The advantage of combining the two components, according to Patel, is that Infinitum was to “software-define the motor.” In other words, through firmware, the OEM can tell the motor exactly what operating point it needs to operate at. (For instance, 10 HP, or 9 HP, or 7 HP, and so forth.)
Motors typically come off the shelf with a NEMA sticker and UL compliance rating. “The UL sticker will say, for example, a 10 HP, 1800 RPM motor will draw 12 amps,” explained Patel. But this presents a limitation, he said, because it denotes the only operating point at which one can modulate the speed. “That means that the machine designer or equipment builder will have to make sure their wiring size is designed for 12 amps, that every one of the motors can support 12 amps, that the circuit breakers have to be designed around 12 amps, the transformers and overload relays and everything else upstream has to be designed for 12 amps,” Patel said.
READ MORE: Understanding Losses in BLDC Motors
But developing a combo solution—motor with the VFD—has meant that the design engineer has more flexibility. “If the customer’s operating point is something other than 10 HP—let’s say it’s a 1,200 RPM application—we can actually tell the motor that its max speed is 1,200 RPM,” said Patel. “But the UL sticker reflects that the motor now is drawing a lower input current. So, instead of 12 amps at 1,200 RPM, now you might be drawing only six amps. And your wiring size can now be reduced.”
There are cost savings to be had in large facilities, too. By one estimation a typical data center relies on 500 motors in their HVAC systems. For a Microsoft or Amazon, or any entity building a data center with more than 1,000 motors, this could be a significant reduction in the capital costs of building that facility. “The upfront cost is reduced just because they use that technology,” pointed out Patel. “There is operational cost reduction because we’re using less energy to provide the same amount of cooling, and so there’s longer-term operational savings.”
Infinitum is rolling out its latest PCB stator motor with specific market segments in mind, said Patel during the briefing with Machine Design.
“We looked out into the market and we said, there’s a lot of places motors are used—everything from a dishwasher motor to 40 motors in a single electric vehicle,” Patel said. “Think about the car windows and the windshield wipers and the fan—there are a whole bunch of the motors there. The point being, there’s a lot of applications this could potentially go into, but we decided to narrow it down to HVAC to start with, industrial second and then mobility third. And within each segment, we found a very receptive audience. Think about most HVAC systems that are running almost 24/7, and so efficiency and sustainability is key for many of these applications,” he said.
Backing from key investors are part-and-parcel of Infinitum’s success story. The start-up reported last year that it had secured $185 million in Series E funding to expand the company, increase production to meet customer demand and drive decarbonization in the industrial sector.
Industrial automation juggernaut Rockwell Automation signed an agreement with Infinitum last year, and is helping the startup break into the industrial space—specifically material handling applications. “Think again about an Amazon distribution center or UPS facility,” said Patel. “They have hundreds of motors on those conveyor systems. Rockwell today supplies a lot of the VFDs that drive those conveyors with our technology, combining the VFD—the electronics, essentially—and the motors to drive those conveyor systems.
READ MORE: VFD Cables Stand Up to Pulse Width Modulation Hazards and Harsh Conditions
Startups like Infinitum are impacted by global economic trends. The global axial flux motor market size is projected to grow from $150.3 million in 2022 to $395.5 million by 2032, at a compound annual growth rate (CAGR) of 10.1%, according to Spherical Insights .
The global HVAC market size was estimated at $16.4 billion in 2022 and is expected to grow to $22.1 billion by 2028 and with a CAGR of 5.10% during the forecast period 2023-2028, according to a Market Data Forecast.
Patel said market size is an important rationale for Infinitum’s decision to focus on commercial HVAC as a core market. Potential applications for the technology are wide-ranging, and may include process compressors, conveyors, pumps, fans, blowers, coolers, compressors, crushers, chippers and grinders.
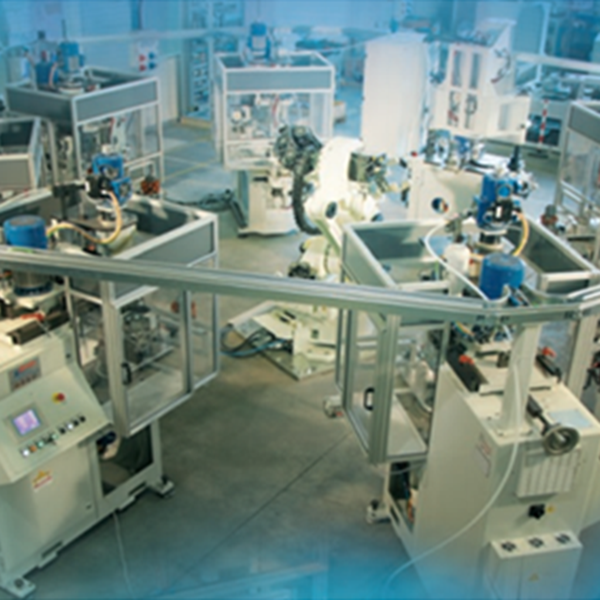
Automatic Line Series Analysts report electric motors will see strong expansion across industries, such as automotive (which is predicted to dominate) and HVAC (systems that manage heating and cooling in industrial and commercial buildings). These industries will expand due to investments in product development.